Amazing Spider Silk
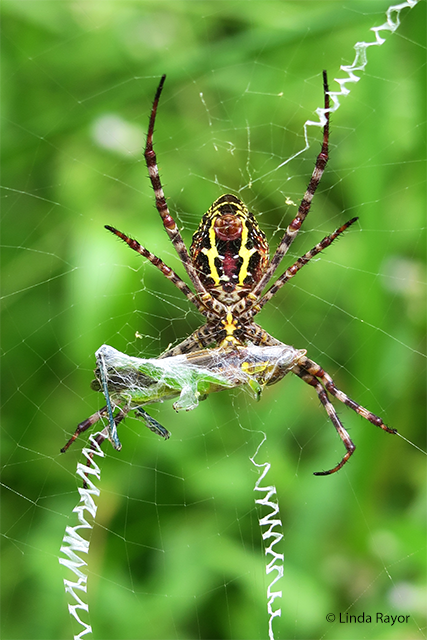
Spider silk has a higher strength-to-density ratio than steel. Spider silk's unmatched combination of strength and toughness have made this protein-based material desirable for many applications ranging from super thin surgical sutures to projectile resistant clothing. Research is currently investigating its remarkable composition and how it could benefit the design of airplanes, bulletproof vests, surgical threads, implants, prostheses, and more.
Although spider silk is an amazing material, it is very difficult to get spiders to produce in quantities sufficient for human use. Spiders simply don’t produce on industrial scales, and are most often predatory of each other if kept together in a production facility. Utah State University researchers have instead found a way to alter the DNA of silkworms so that spider proteins could be incorporated into the silk threads produced by the silkworms. This new silk has double the strength and far more elasticity than normal silkworm silk and can also be mass-produced. The resulting material successfully stopped a slow-moving .22-caliber bullet using just four layers. Thirty-three layers of Aramid, a synthetic polymid, are used to make today’s standard body armor.
Similar to the ones the researchers at Utah State created, Kraig Biocraft Laboratories in Lansing, Michigan genetically engineered silkworms to produce spider silk as well. Kraig Biocraft Labs announced in 2018 that they are calling this new fabric “Dragon Silk” and are aiming to use it in the design of lightweight and flexible body armor, particularly for the groin area. In search of even more robust “spider silk” (made by non-spiders) researchers at Washington University in St. Louis have engineered bacteria that produce a biosynthetic spider silk with performance on par with its natural counterparts. Just as importantly, their research revealed that tensile strength and toughness of spider silk remains positively correlated with its molecular weight -- i.e. the bigger the molecule, the stronger the silk!
At Aalto University and VTT Technical Research Centre in Finland, researchers combined birch wood cellulose fibers and silk proteins to create a firm and resilient material similar to plastic with promise for use in medical applications such as surgical fibers, in the textile industry, and in packaging. Unlike plastic, it is actually biodegradable. Other research has made strides in utilizing silk to create a bioresorbable composite material that could be an alternative to titanium and other implants used to help in healing of bone fractures, but which would then be absorbed by the body to avoid the need for surgical extraction or other complications from a permanent implant. Super thin sutures made from bundled spider silk holds similar potential for extreme strength with the added benefit of being absorbed by the body when no longer needed.
"Bigger proteins, stronger threads: Synthetic spider silk: Engineering scientists use bacteria to create biosynthetic silk stronger and more tensile than before." ScienceDaily. www.sciencedaily.com/releases/2018/08/180821094234.htm (accessed September 19, 2019)
Aalto University. "Combination of wood fibers and spider silk could rival plastic." ScienceDaily. www.sciencedaily.com/releases/2019/09/190916101845.htm (accessed September 19, 2019)
Heimbach, Bryant, Beril Tonyali, Dianyun Zhang, and Mei Wei. 2018. “High Performance Resorbable Composites for Load-Bearing Bone Fixation Devices.” Journal of the Mechanical Behavior of Biomedical Materials 81 (May): 1-9. https://doi.org/10.1016/J.JMBBM.2018.01.031.
"Bundles of Spider Silk, Braided into Sutures, Resist Basic Cyclic Tests: Potential Use for Flexor Tendon Repair". Kathleen Hennecke, Joern Redeker, Joern W. Kuhbier, Sarah Strauss, Christina Allmeling, Cornelia Kasper, Kerstin Reimers, Peter M. VogtPLoS One. 2013; 8(4): e61100. Published online 2013 Apr 17. doi: 10.1371/journal.pone.0061100